The Complete Guide to Aluminum Anodizing: Essential Facts
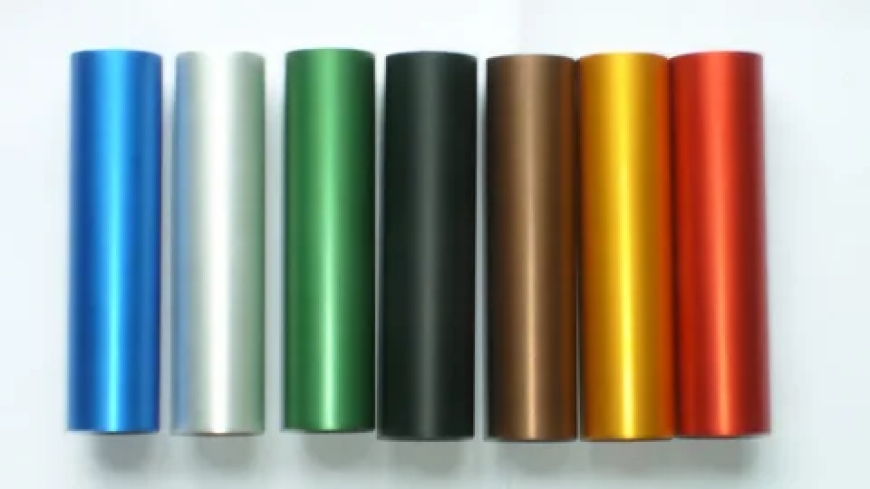
One of the most outstanding surface treatment processes in current day manufacturing is aluminum anodizing. It is an electrochemical process, which can turn out of ordinary aluminum, so that it can be used as a material of extraordinary properties, with the passport that is in the vast majority of industries. Whether it is the beautiful sheen on your touch screen phone, the tough covering on an aircraft component, or the light covering on an appliance that has enhanced performance, anodized aluminum is everywhere, and you hardly ever give it a thought. Knowing this process creates an entrance to the marvel of engineering creation, which preserves and adds value to the entire world of aluminum products.
1.Understanding the Fundamental Process
Aluminum anodizing is an electrochemical process that also achieves protective oxide on aluminum surfaces as a result of controlled oxidation. Anodizing is not painting or coating, actually, anodizing operation irreversibly alters the aluminum surface to be covered into a protective layer. The actual procedure entails submerging aluminium components into an electrolytic solution (traditionally, it is sulfuric acid), and running an electric current through the arrangement. This current reduces oxygen ions to aluminum ions on the surface of the aluminum atoms, resulting in the formation of aluminum oxide. The thickness and properties of such an oxide layer can be carefully controlled by variation of parameters (voltage, current density, temperature, processing time), and anodizing can be considered a science as well as an art.
2.The Science Behind Enhanced Durability
The aluminum oxide film formed by the anodizing process forms a far stronger resistance to abrasion, corrosion and environmental destruction hence making the aluminum oxide film far stronger compared to the original aluminum layer. and this oxide coating is so hard, in fact, that steel, at 9 on the Moh hardness scale, is nothing to the oxide, which measures between 2.5 and 3 in terms of hardness, on a par with aluminum. The anodized surface will be non-conductive, that is, it will not need much reaction to most chemicals or environmental substances that usually promote corrosion. The change can be attributed to the fact that the oxide layer is non-porous at the surface area and has microscopic pores that protrude into the aluminum substrate. This can be done by sealing these pores by use of some form of treatment which forms a barrier, thus providing the underlying metal protection against corrosion over decades when exposed to normal environments.
3.Color Possibilities and Aesthetic Applications
The color produced in anodizing is one of the most attractive features of the process. The colors are durable and become an intrinsic property of the metal. The dyes and the pigments can be sealed on the surface as the pores of the anodized layer can absorb them. This implies that the color can not chip, peel, or wear off, as in the case of paint or powder coating. The color is various, but goes between natural colors (silver, bronze) as well as bright blues, reds, gold, and black. The sealing procedure takes place after the coloring procedure, and the dye is allowed to penetrate deep into the porous oxide layer. There are colors produced by the anodizing process itself, e.g., bronze color by certain electrolyte compositions.
4.Environmental Benefits and Sustainability
Anodizing is actually one of the most eco-friendly surface finishing processes that exists these days. No heavy metals are used, and no hazardous blowdown air is produced, and there is little wastage. In anodizing, no foreign material is introduced into the surface as in painting or plating processes, but rather the exact arrangement of the existing aluminum atoms is rearranged to form the protective layer. The anodizing solutions can be easily recycled and reutilised many times, and it does not consume much energy when compared to other surface finishing processes. Also, anodized aluminum can be recycled, because the oxide layer is chemically the same as the oxide in nature, aluminum oxide.
5.Industrial Applications Across Multiple Sectors
The versatility of the anodized aluminum enables it to be invaluable to other industries, each of which takes full advantage of the multiple characteristics that the process produces. These anodized aluminum parts are employed in the aerospace outfits where those components are not susceptible to corrosion even in harsh atmospheric conditions, but those are lightweight, and this attribute is critical in fuel consumptions. The usage of anodized aluminum may be either practical or aesthetic in the car industry as would be the case of parts of the engine which have to be resistant to corrosion or just the fancy outlooks. The producers of the electronics equipment apply anodised aluminum to cover its equipment (in housing mode) in order to achieve a shielding effect against electromagnetic energy, cooling, and giving the high end decorating effects to its products.
6.Types of Anodizing Processes Available
Several types of anodizing processes can be used, with different purposes and final applications involved. The most frequent one, sulfuric acid anodizing, provides a more decorative layer of comparatively thin coating to apply to the vast majority of applications. Hard anodizing, or Type III, produces coatings that are many times thicker and better suited for wear-resistant applications. Chromic acid anodizing is used to provide a thin coat with very good paint adhesion characteristics and as a primer on painted applications. The anodizing of phosphoric acids forms a special surface structure in this case, which is suitable when it comes to bonding. The two processes use varying electrolyte solutions, conditions, and the resulting properties.
7.Quality Control and Testing Standards
Tough testing and adherence to the standards have to be followed to sustain the same level of quality of anodized aluminum. The instruments involved are to ensure that the coating on the surface is of the right thickness by measuring it as the latter will influence the longevity and effectiveness. Spectrophotometers used with visual evaluation against master standards are used to assess color consistency. Tests of adhesion will make the coating stick to the substrate correctly. Corrosion resistance is examined in the tests by subjecting parts to a corrosive setting over a lengthy duration, and then subjecting them to various salts by a method called salt spray testing.
Conclusion
Anodizing of aluminum is an epitome of science, technology, and practicality, which has transformed our approach to protecting and upgrading any aluminum product with JM Aluminium. In its basic electrochemical process or its various usages in multiple industries, anodization is still proving to be a worthy process through its levels of superior durability, beauty, and environmental responsibility.